Technologies
Our specialty and strength is versatility in both the materials that we are able to processe and the technologies required for metal processing. Our product development department is ready to advise customers on the selection of suitable materials and product construction in order to achieve the best price-quality ratio. This, in turn, is complemented by product development capability and the ability to design and also manufacture tools and jigs necessary for series work. Through our extensive and global network of suppliers, we are also able to source all other necessary components to complete your product.
Technologies
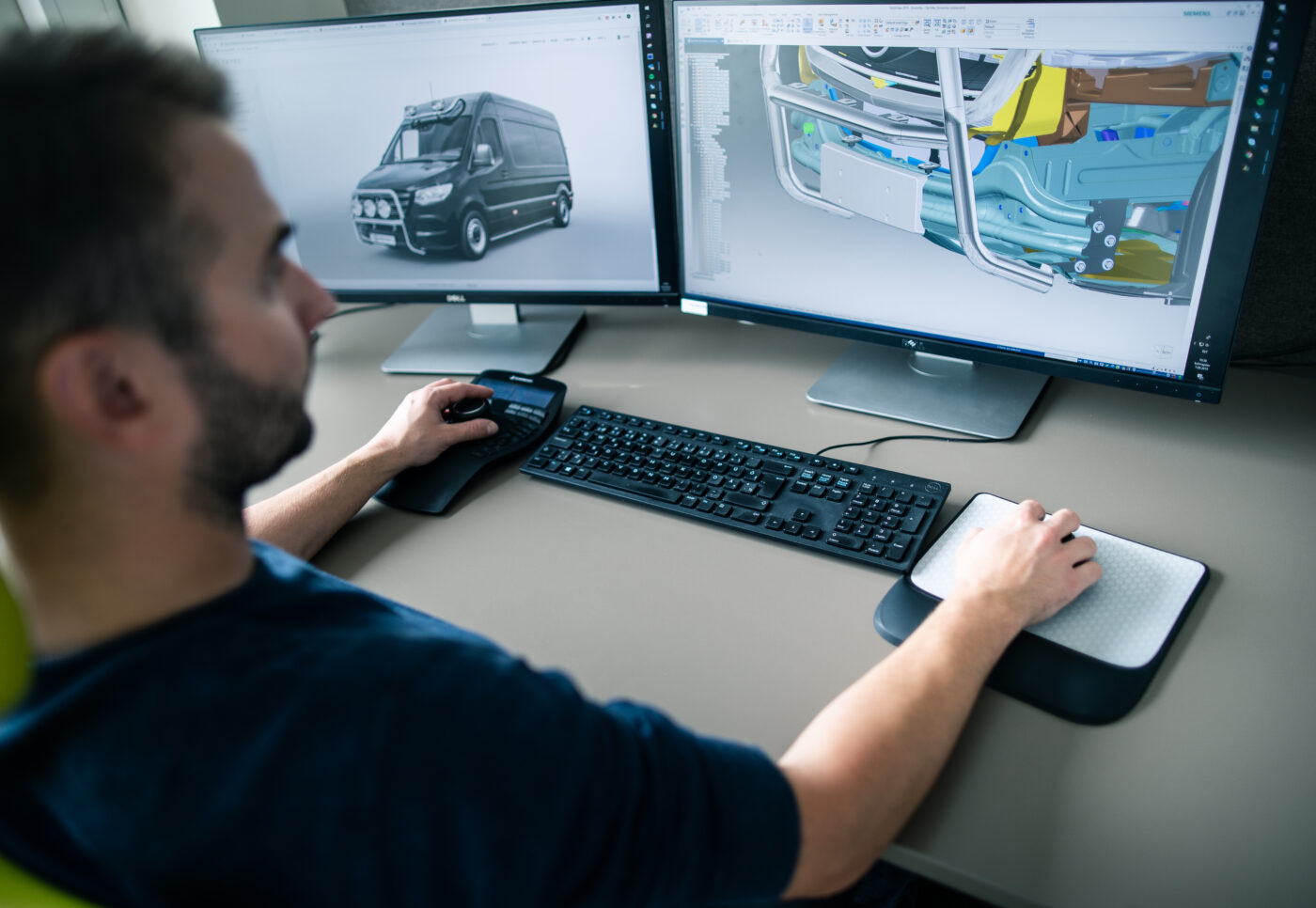
Consulting on product development
Among our clients are globally renowned companies with long-term experience in developing their own products. It is unlikely that we would be able to advise them on how to improve the functional properties or durability of the products. However, it may be possible that our knowledge of the possibilities of manufacturing such products is more recent than that of the owner of the product, and the tips received from us may be helpful in reducing the manufacturing costs of the products without making concessions at the expense of other product properties.
Our customers are also newly started companies that only have preliminary product sketches and/or a handcrafted prototype. We are likely to be able to advise such enterprises on the selection of suitable construction materials as well as the selection of the technological solution of the product nodes, which help to create a high-quality and sustainable product at reasonable costs considering the planned sales volumes.
We can read and, if necessary, modify all different models and drawings transmitted in 3D and vector format. If necessary, we are ready to create drawings of individual parts based on the models and supplement them with additional information, which may be important in terms of a high-quality and fast manufacturing process.
Our customers are also newly started companies that only have preliminary product sketches and/or a handcrafted prototype. We are likely to be able to advise such enterprises on the selection of suitable construction materials as well as the selection of the technological solution of the product nodes, which help to create a high-quality and sustainable product at reasonable costs considering the planned sales volumes.
We can read and, if necessary, modify all different models and drawings transmitted in 3D and vector format. If necessary, we are ready to create drawings of individual parts based on the models and supplement them with additional information, which may be important in terms of a high-quality and fast manufacturing process.
Consulting on product development
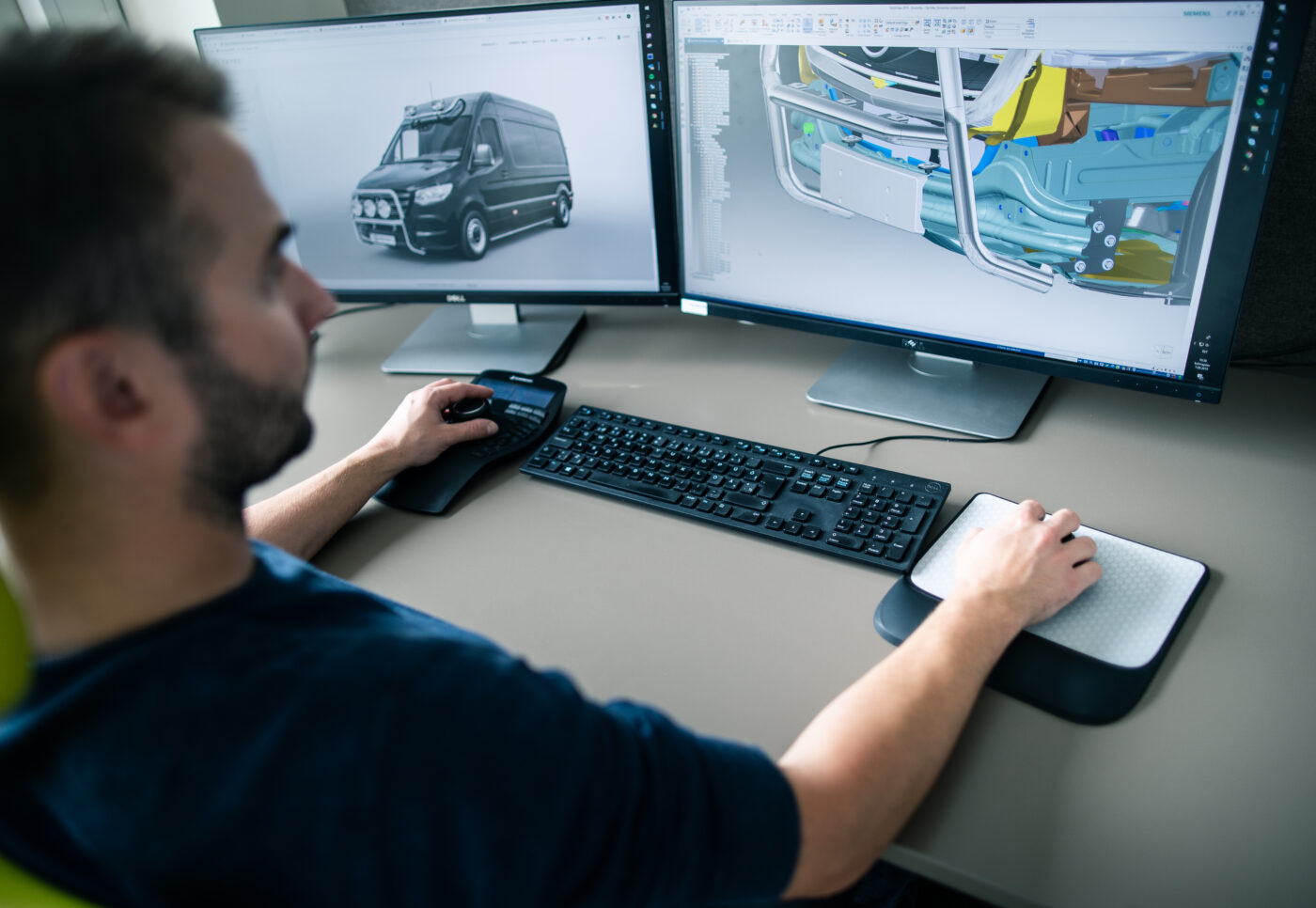
Consulting on technology
Reasonable manufacturing technology for manufacturing products is dependent on expected sales volumes. It is a well-known rule that by investing more in product-specific tools and remedies, it is possible to achieve lower manufacturing costs in the future. At the same time, not all customers may have the necessary financial capacity and risk courage to make such investments in the initial phase of a new product's life cycle. We have flexible manufacturing technologies for most work operations, which allow you to achieve the required result with a minimum initial investment, as well as industrial technologies that require an initial investment in special tools, but then ensure lower production costs. We can be here as an advisor to our customers, where a reasonable risk limit could be located between the cost price of the product and the required initial investment.
If the product manufacturing technology is coordinated with the customer, all the details of its manufacturing - materials used, work operations and quality (control) requirements are described in detail in a digital product assembly, which ensures the necessary basic data for the future procurement of input components and error-free production.
If the product manufacturing technology is coordinated with the customer, all the details of its manufacturing - materials used, work operations and quality (control) requirements are described in detail in a digital product assembly, which ensures the necessary basic data for the future procurement of input components and error-free production.
Consulting on technology
Manufacturing and maintenance of tools and work aids
If, as a result of the discussions with the customer, a common point of view has been reached on the expediency of manufacturing tools and remedies, then we are able to organize both their design and manufacture with our own forces. We can manufacture cutting and bending dies, welding, assembly and inspection jigs.
Our in-house instrument unit not only allows us to speed up the product introduction process and better control their costs, but it also gives us an advantage in the future for maintenance, repair and modification of work aids.
You can find out more about our toolmaking competencies here:
TOOL CONSTRUCTION
Our in-house instrument unit not only allows us to speed up the product introduction process and better control their costs, but it also gives us an advantage in the future for maintenance, repair and modification of work aids.
You can find out more about our toolmaking competencies here:
TOOL CONSTRUCTION
Manufacturing and maintenance of tools and work aids
Production of tube parts
We weld various types of non-alloy steel, stainless steel, and aluminium. We use manual arc welding stations, semi-automatic systems as well as multi-headed welding robots. The company is recognised as a certified provider of welding tasks according to the ISO 3834–2 standard. Welding is one of our key processes. Metec employs over 30 welders. We design and prepare required jigs for manual and robotic welding.
Production of tube parts
Production of sheet metal parts
There are thousands of companies in the world that have the ability to offer sheet metal laser cutting and bending services. A special feature of Metec is the ability to choose between laser cutting - bending technology, which requires a minimum initial investment, and pressing - stamping technology, which is more suitable and cost-effective for larger batches and/or precision requirements, due to the accuracy requirements and quantities of the parts. The presence of various technologies for removing processing residues, over-processing holes or threading complements the list of technologies necessary for high-quality production of sheet parts.
Production of sheet metal parts
CNC machining
Our machine park includes several dozen CNC turning and milling machines with varying capabilities. Our range of lathes extends from simpler single-spindle machines to dual-spindle machines with two turrets. We can produce parts with a maximum diameter of ⌀350 and a length of 600 mm. We also have a wide selection of milling machines capable of simultaneous 5-axis machining and processing parts up to 1500 x 700 x 500 mm in size.
Some of our machining centers are equipped with loading systems or robots, which reduce the number of manual operations and ensure higher efficiency. All our machines use Siemens control software, which ensures production flexibility and adherence to customer delivery requirements.
We process a wide variety of materials such as plastics, aluminum, stainless steel, as well as castings or welded assemblies. For smaller production batches, we can also use universal turning, milling, grinding, and EDM machines
Some of our machining centers are equipped with loading systems or robots, which reduce the number of manual operations and ensure higher efficiency. All our machines use Siemens control software, which ensures production flexibility and adherence to customer delivery requirements.
We process a wide variety of materials such as plastics, aluminum, stainless steel, as well as castings or welded assemblies. For smaller production batches, we can also use universal turning, milling, grinding, and EDM machines
CNC machining
Procurement of components
The end products we manufacture also include a large number of plastic parts, wire harnesses and electronic, pneumatic and hydraulic components, some of which can be standard and some designed according to the customer's special requirements. On a daily basis, we cooperate with companies specializing in the design and manufacture of such parts, in order to be able to offer you a completely ready-to-use product.
Procurement of components
Welding
Next to pipe processing, our welding skills can be considered another key competence with which we can positively differentiate ourselves from our competitors.
We weld various carbon steels, stainless steel and aluminum, using either MIG-MAG, TIG or laser welding process depending on the need. Manual welding workplaces, semi-automatic welding machines and multi-headed welding robots are in use. The company is recognized as an ISO 3834-2 certified welding contractor. We also have the ISO EN 15085-2:2007 welding certificate required in the railway industry.
We weld various carbon steels, stainless steel and aluminum, using either MIG-MAG, TIG or laser welding process depending on the need. Manual welding workplaces, semi-automatic welding machines and multi-headed welding robots are in use. The company is recognized as an ISO 3834-2 certified welding contractor. We also have the ISO EN 15085-2:2007 welding certificate required in the railway industry.
Welding
Surface finish
We use a wide range of different technologies to give stainless steel or black metal parts, sub-assemblies or final products the required aesthetic appearance and corrosion resistance. In the case of ready-to-use products, which make up 70% of our sales revenue, surface finishing is unavoidable. We also perform surface finishing on half of the parts or sub-assemblies, which we supply as inputs to other production units. For stainless steel parts or assemblies, we can perform mechanical grinding and polishing, shot peening, electropolishing and electrochemical etching, wet or powder painting if necessary.
For the finishing of parts made of carbon steel, we use shot blasting, wet and powder painting, after which it is possible to cover the parts with either a galvanic or Oxcilan protective layer to increase their corrosion resistance. In cooperation with our subcontractors, we can also offer e-coat and hot-dip galvanizing for steel parts and anodizing for aluminum parts.
For the finishing of parts made of carbon steel, we use shot blasting, wet and powder painting, after which it is possible to cover the parts with either a galvanic or Oxcilan protective layer to increase their corrosion resistance. In cooperation with our subcontractors, we can also offer e-coat and hot-dip galvanizing for steel parts and anodizing for aluminum parts.
Surface finish
Compilation
We perform assembly of mechanical, hydraulic and electrical components and functional testing of final products. We have a separate ESD assembly area for the assembly of electronic components sensitive to static electricity.
Compilation
Quality control
70% of the products manufactured by Tarmetec are end products, i.e. they are not made as inputs for other manufacturing plants but are ready for end use. This fact means that no one controls the quality of our work more, which in turn puts higher demands on our internal control procedures.
Quality control starts as soon as the materials or product components arrive at the factory. The frequency of the inspection is determined either on the basis of an analysis of the probability of the occurrence of an error or on the basis of the customer's requirements. To carry out control measurements, we use portable or stationary measuring devices or special-purpose measuring devices that meet the accuracy requirements. The measurement results are recorded in the ERP software by the employee who performed the measurement process.
All non-conformities are recorded and processed by the quality department according to the German automotive industry standard (8D – Report).
Quality control starts as soon as the materials or product components arrive at the factory. The frequency of the inspection is determined either on the basis of an analysis of the probability of the occurrence of an error or on the basis of the customer's requirements. To carry out control measurements, we use portable or stationary measuring devices or special-purpose measuring devices that meet the accuracy requirements. The measurement results are recorded in the ERP software by the employee who performed the measurement process.
All non-conformities are recorded and processed by the quality department according to the German automotive industry standard (8D – Report).